โดยทั่วไปวิธีการเคลือบของโฟโตรีซิสต์จะแบ่งออกเป็นการเคลือบแบบหมุน การเคลือบแบบจุ่ม และการเคลือบแบบม้วน ซึ่งโดยทั่วไปจะใช้การเคลือบแบบหมุนมากที่สุด ด้วยการเคลือบแบบหมุน สารต้านทานแสงจะถูกหยดลงบนวัสดุพิมพ์ และสามารถหมุนวัสดุพิมพ์ได้ด้วยความเร็วสูงเพื่อให้ได้ฟิล์มสารต้านทานแสง หลังจากนั้นสามารถรับฟิล์มแข็งได้โดยการให้ความร้อนบนจานร้อน การเคลือบแบบหมุนเหมาะสำหรับการเคลือบตั้งแต่ฟิล์มบางพิเศษ (ประมาณ 20 นาโนเมตร) ไปจนถึงฟิล์มหนาประมาณ 100 ไมโครเมตร คุณลักษณะของมันคือความสม่ำเสมอที่ดี ความหนาของฟิล์มสม่ำเสมอระหว่างเวเฟอร์ มีข้อบกพร่องเล็กน้อย ฯลฯ และได้ฟิล์มที่มีประสิทธิภาพการเคลือบสูง
กระบวนการเคลือบแบบสปิน
ในระหว่างการเคลือบแบบหมุน ความเร็วการหมุนหลักของซับสเตรตจะกำหนดความหนาของฟิล์มของโฟโตรีซิสต์ ความสัมพันธ์ระหว่างความเร็วในการหมุนและความหนาของฟิล์มเป็นดังนี้:
สปิน=kTn
ในสูตร Spin คือความเร็วในการหมุน T คือความหนาของฟิล์ม k และ n เป็นค่าคงที่
ปัจจัยที่ส่งผลต่อกระบวนการเคลือบแบบสปิน
แม้ว่าความหนาของฟิล์มจะถูกกำหนดโดยความเร็วในการหมุนหลัก แต่ก็ยังเกี่ยวข้องกับอุณหภูมิห้อง ความชื้น ความหนืดของโฟโตรีซิสต์ และประเภทโฟโตรีซิสต์ด้วย การเปรียบเทียบเส้นโค้งการเคลือบโฟโตรีซิสต์ประเภทต่างๆ แสดงในรูปที่ 1
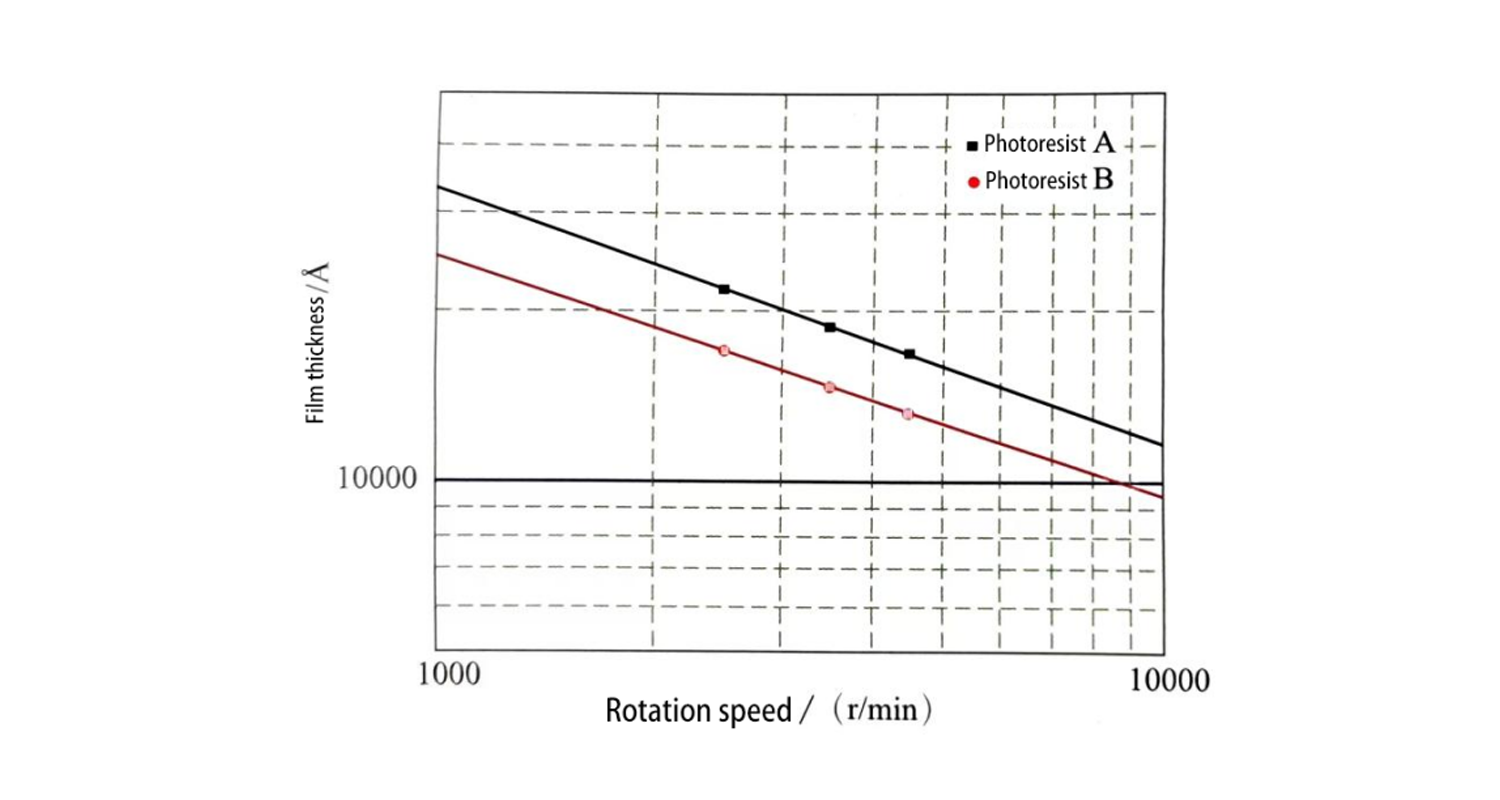
รูปที่ 1: การเปรียบเทียบเส้นโค้งการเคลือบโฟโตรีซิสต์ประเภทต่างๆ
อิทธิพลของเวลาการหมุนหลัก
ยิ่งเวลาการหมุนหลักสั้นลง ความหนาของฟิล์มก็จะยิ่งหนาขึ้น เมื่อเวลาการหมุนหลักเพิ่มขึ้น ฟิล์มก็จะบางลง เมื่อเกิน 20 วินาที ความหนาของฟิล์มยังคงไม่เปลี่ยนแปลงเกือบ ดังนั้นเวลาหมุนหลักมักจะเลือกไว้มากกว่า 20 วินาที ความสัมพันธ์ระหว่างเวลาการหมุนหลักและความหนาของฟิล์มแสดงในรูปที่ 2
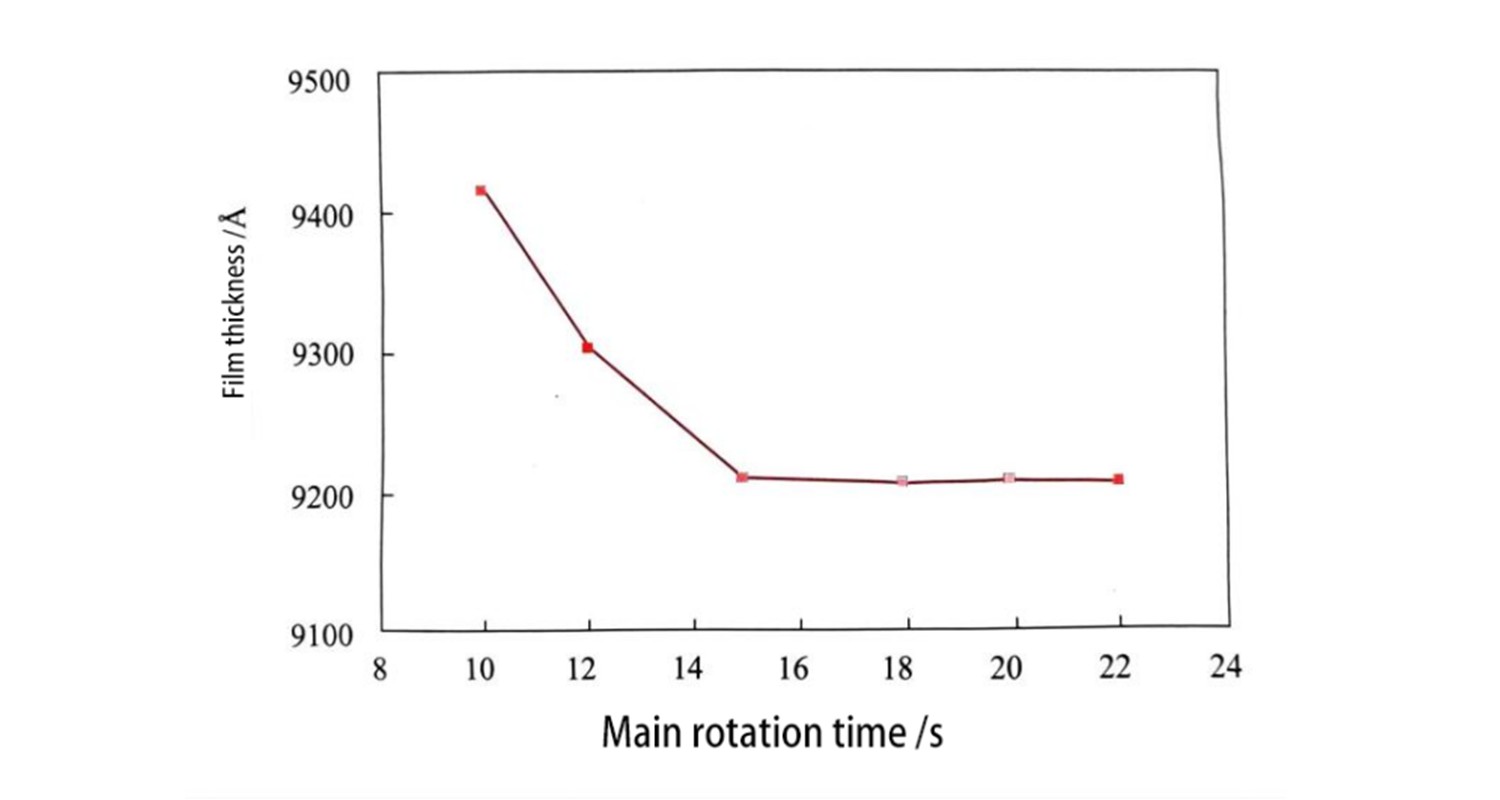
รูปที่ 2: ความสัมพันธ์ระหว่างเวลาการหมุนหลักและความหนาของฟิล์ม
เมื่อโฟโตรีซีสต์ถูกหยดลงบนซับสเตรต แม้ว่าความเร็วในการหมุนหลักที่ตามมาจะเท่ากัน ความเร็วในการหมุนของซับสเตรตในระหว่างการหยดจะส่งผลต่อความหนาของฟิล์มขั้นสุดท้าย ความหนาของฟิล์มโฟโตรีซิสต์จะเพิ่มขึ้นตามความเร็วการหมุนของสารตั้งต้นที่เพิ่มขึ้นในระหว่างการหยด ซึ่งเป็นผลมาจากอิทธิพลของการระเหยของตัวทำละลายเมื่อโฟโตรีซิสต์ถูกกางออกหลังจากการหยด รูปที่ 3 แสดงความสัมพันธ์ระหว่างความหนาของฟิล์มและความเร็วในการหมุนหลักที่ความเร็วการหมุนของวัสดุพิมพ์ที่แตกต่างกันระหว่างการหยดของโฟโตรีซีสต์ จากรูปจะเห็นได้ว่าเมื่อความเร็วการหมุนของซับสเตรตหยดเพิ่มขึ้น ความหนาของฟิล์มจะเปลี่ยนไปเร็วขึ้น และความแตกต่างจะชัดเจนมากขึ้นในบริเวณที่มีความเร็วการหมุนหลักต่ำลง
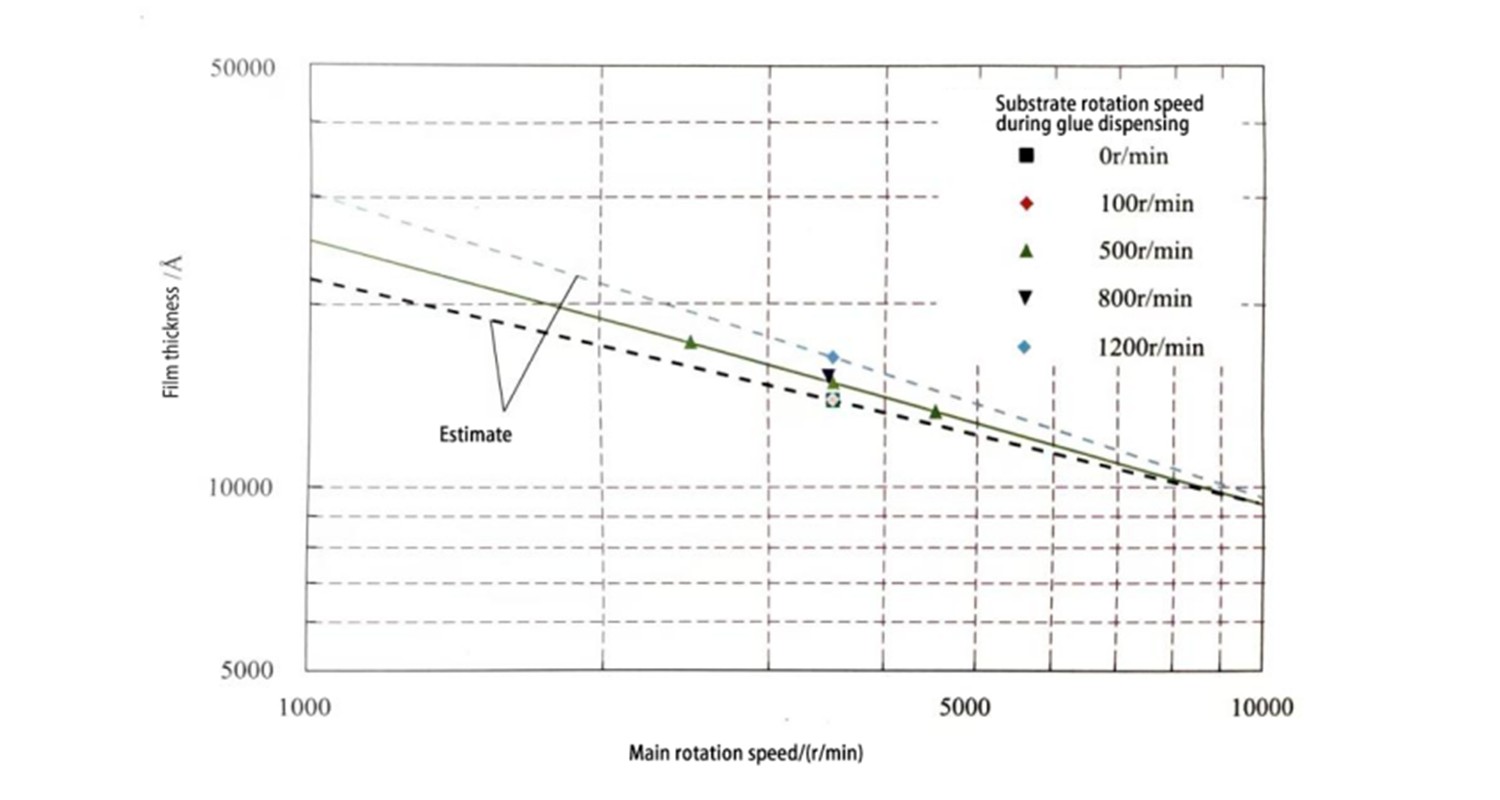
รูปที่ 3: ความสัมพันธ์ระหว่างความหนาของฟิล์มและความเร็วการหมุนหลักที่ความเร็วการหมุนของสารตั้งต้นที่แตกต่างกันในระหว่างการจ่ายสารต้านทานแสง
ผลกระทบของความชื้นระหว่างการเคลือบ
เมื่อความชื้นลดลง ความหนาของฟิล์มจะเพิ่มขึ้น เนื่องจากความชื้นที่ลดลงจะส่งเสริมการระเหยของตัวทำละลาย อย่างไรก็ตาม การกระจายความหนาของฟิล์มไม่เปลี่ยนแปลงอย่างมีนัยสำคัญ รูปที่ 4 แสดงความสัมพันธ์ระหว่างความชื้นและการกระจายความหนาของฟิล์มในระหว่างการเคลือบ
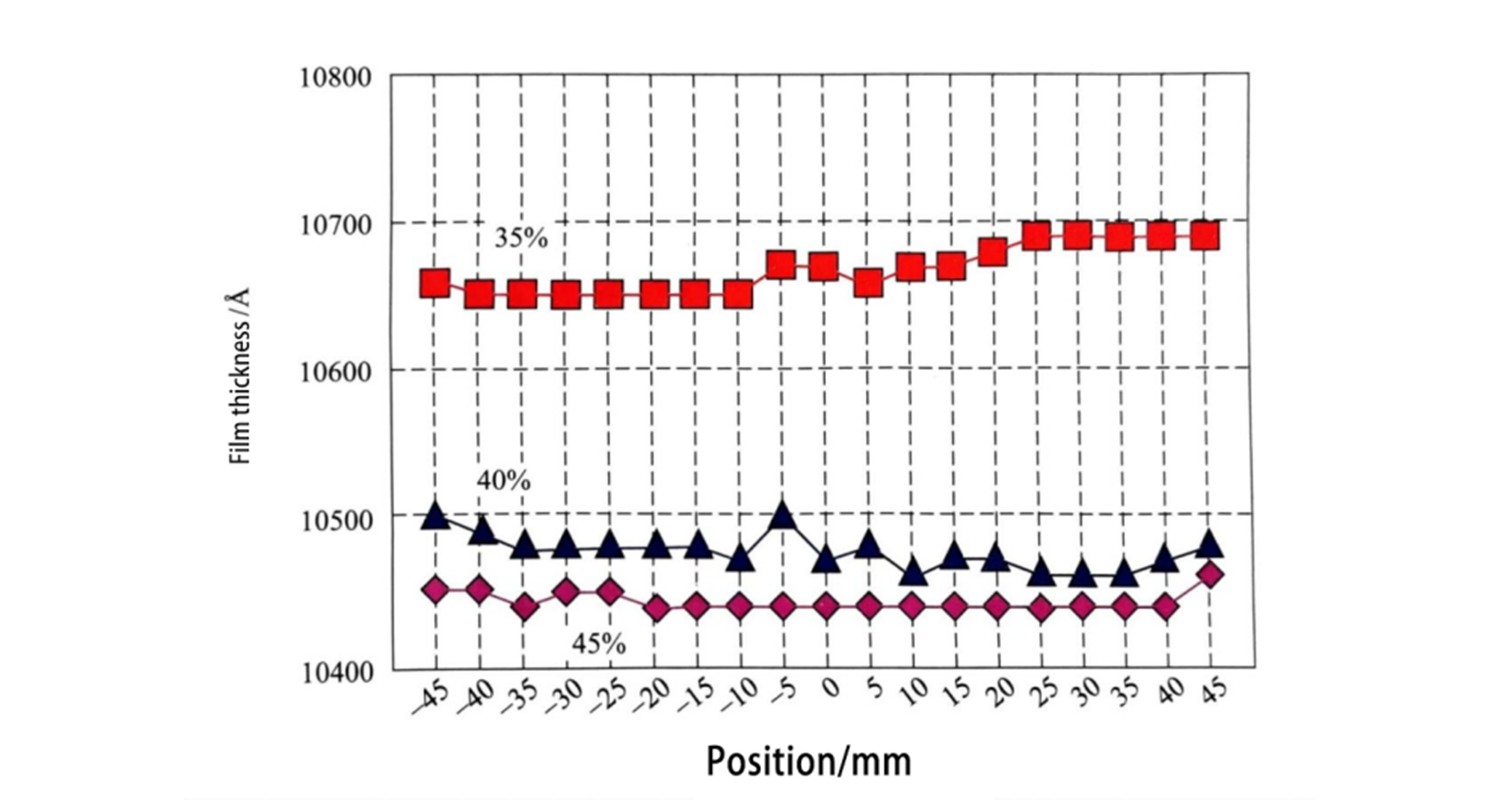
รูปที่ 4: ความสัมพันธ์ระหว่างความชื้นและการกระจายความหนาของฟิล์มระหว่างการเคลือบ
ผลกระทบของอุณหภูมิระหว่างการเคลือบ
เมื่ออุณหภูมิภายในอาคารสูงขึ้น ความหนาของฟิล์มจะเพิ่มขึ้น จะเห็นได้จากรูปที่ 5 ว่าการกระจายความหนาของฟิล์มไวแสงเปลี่ยนจากนูนไปเป็นเว้า เส้นโค้งในภาพยังแสดงให้เห็นว่าได้รับความสม่ำเสมอสูงสุดเมื่ออุณหภูมิภายในอาคารอยู่ที่ 26°C และอุณหภูมิของตัวต้านทานแสงคือ 21°C
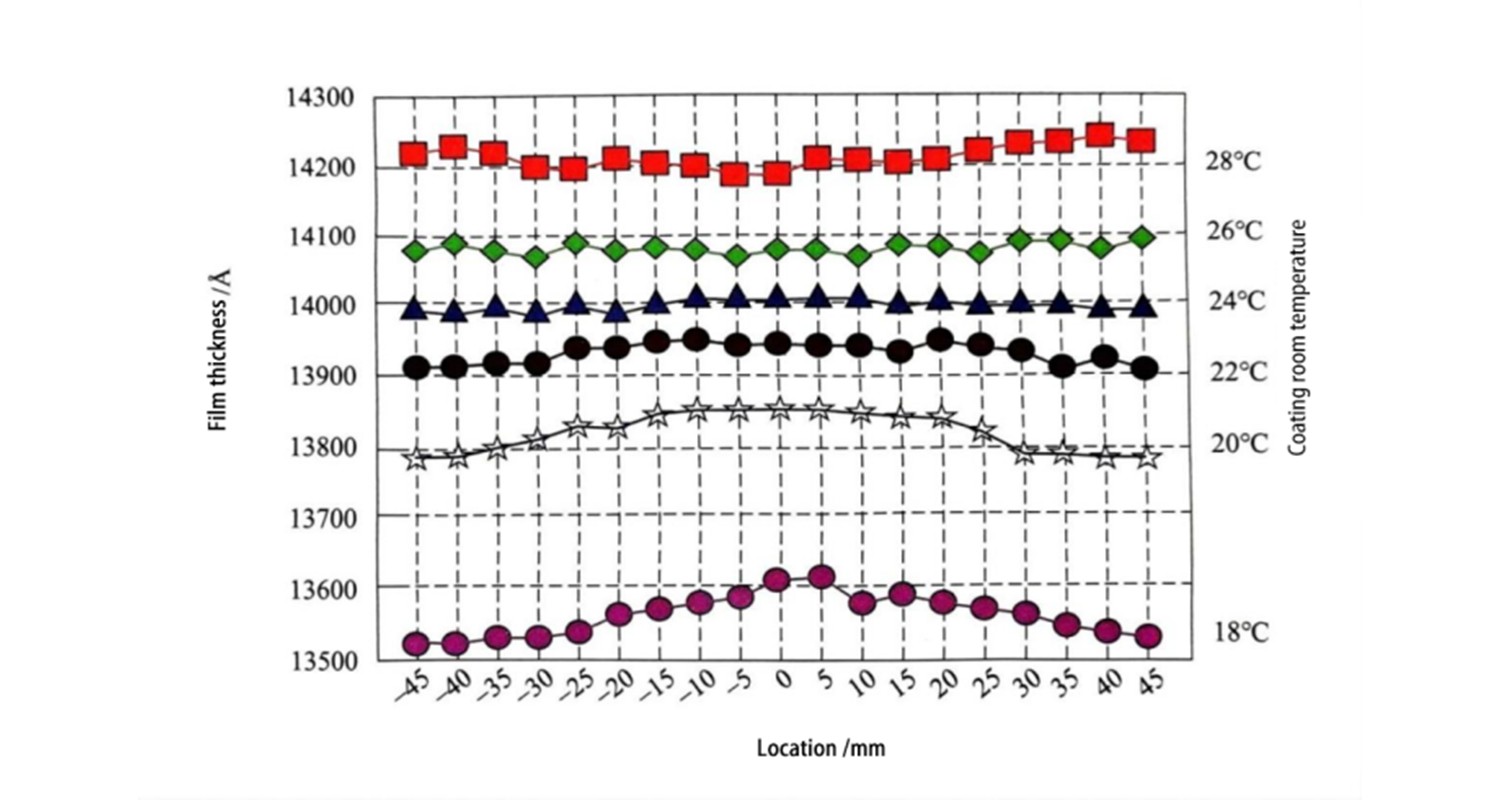
รูปที่ 5: ความสัมพันธ์ระหว่างอุณหภูมิและการกระจายความหนาของฟิล์มระหว่างการเคลือบ
ผลกระทบของความเร็วไอเสียระหว่างการเคลือบ
รูปที่ 6 แสดงความสัมพันธ์ระหว่างความเร็วไอเสียและการกระจายความหนาของฟิล์ม ในกรณีที่ไม่มีไอเสีย แสดงว่าจุดศูนย์กลางของแผ่นเวเฟอร์มีแนวโน้มที่จะข้นขึ้น การเพิ่มความเร็วไอเสียจะช่วยเพิ่มความสม่ำเสมอ แต่ถ้าเพิ่มมากเกินไป ความสม่ำเสมอจะลดลง จะเห็นได้ว่ามีค่าความเร็วไอเสียที่เหมาะสมที่สุด
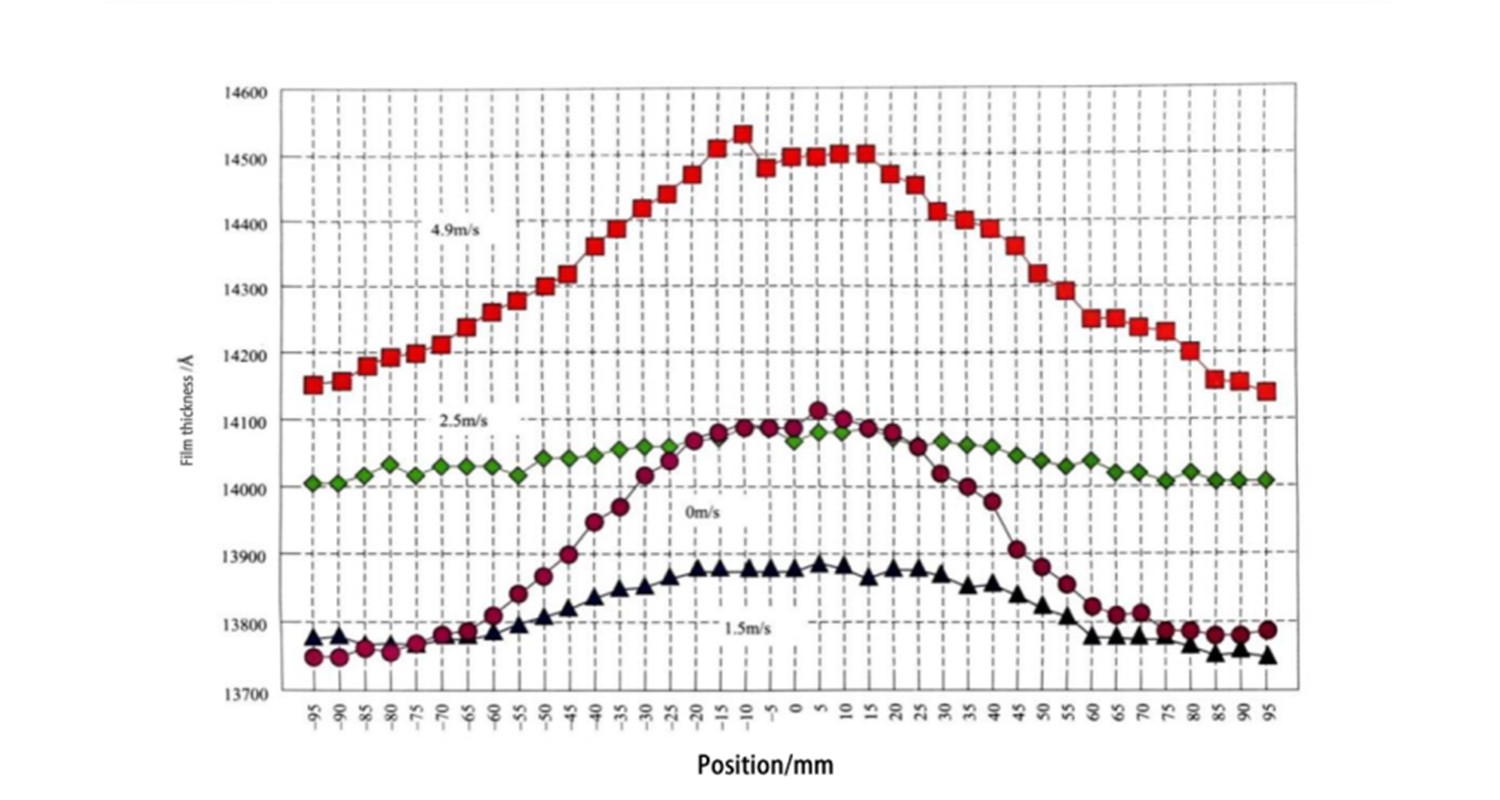
รูปที่ 6: ความสัมพันธ์ระหว่างความเร็วไอเสียและการกระจายความหนาของฟิล์ม
การรักษา HMDS
เพื่อให้ไวแสงสามารถเคลือบได้มากขึ้น เวเฟอร์จะต้องได้รับการบำบัดด้วยเฮกซาเมทิลไดซิลาเซน (HMDS) โดยเฉพาะอย่างยิ่งเมื่อมีความชื้นติดอยู่ที่พื้นผิวของฟิล์ม Si ออกไซด์ จะเกิดไซลานอลขึ้น ซึ่งช่วยลดการยึดเกาะของสารต้านทานแสง เพื่อขจัดความชื้นและสลายไซลานอล โดยปกติแล้วแผ่นเวเฟอร์จะถูกให้ความร้อนที่ 100-120°C และมีการนำหมอก HMDS มาใช้เพื่อทำให้เกิดปฏิกิริยาทางเคมี กลไกการเกิดปฏิกิริยาแสดงในรูปที่ 7 ด้วยการบำบัด HMDS พื้นผิวที่ชอบน้ำที่มีมุมสัมผัสเล็ก ๆ จะกลายเป็นพื้นผิวที่ไม่ชอบน้ำที่มีมุมสัมผัสขนาดใหญ่ การทำความร้อนแผ่นเวเฟอร์จะทำให้มีการยึดเกาะของโฟโตรีซิสต์สูงขึ้น
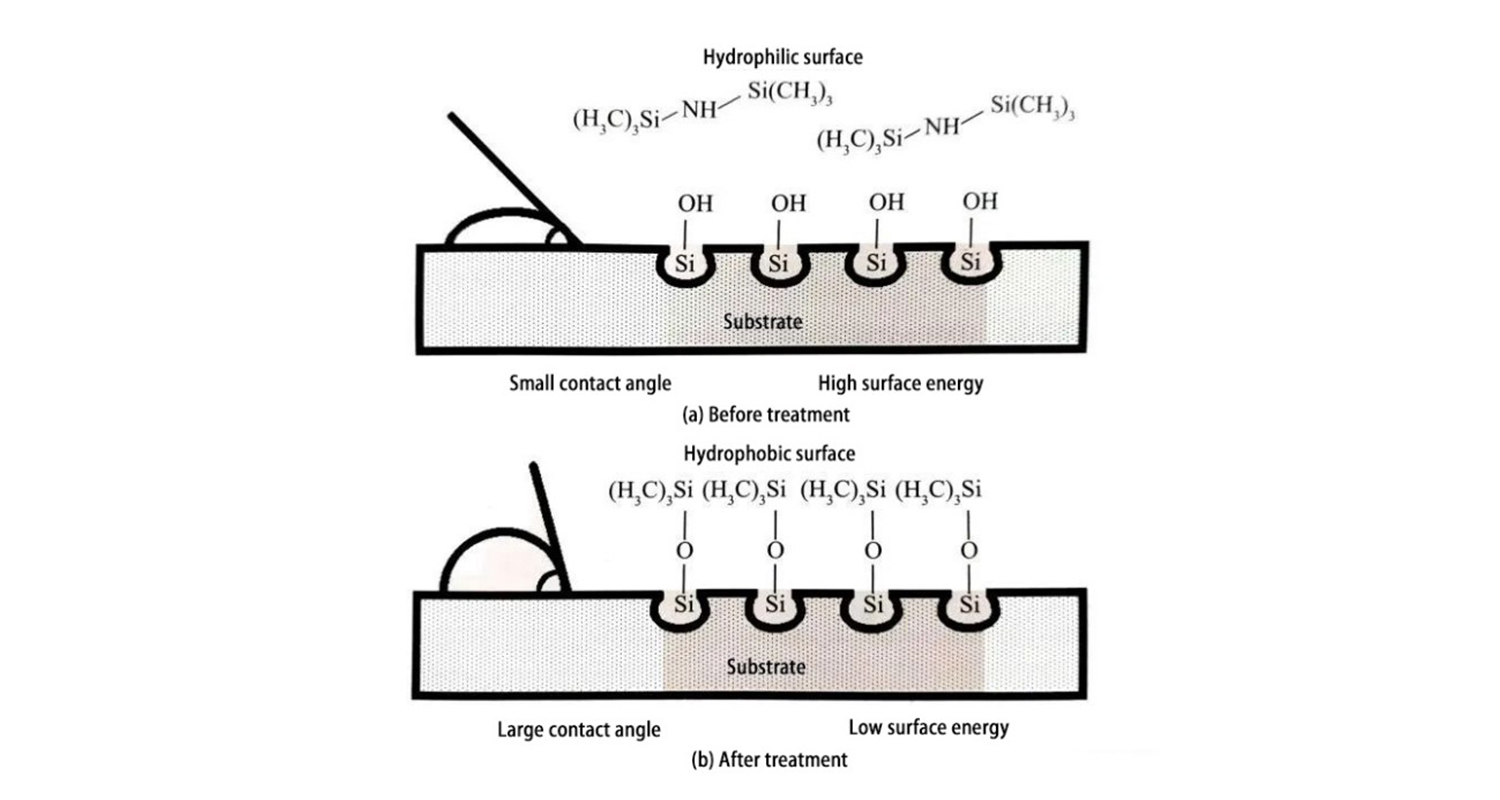
รูปที่ 7: กลไกปฏิกิริยา HMDS
สามารถสังเกตผลของการรักษา HMDS ได้โดยการวัดมุมสัมผัส รูปที่ 8 แสดงความสัมพันธ์ระหว่างเวลาการบำบัด HMDS และมุมสัมผัส (อุณหภูมิการบำบัด 110°C) วัสดุพิมพ์คือ Si เวลาการรักษา HMDS มากกว่า 1 นาที มุมสัมผัสมากกว่า 80° และผลการรักษามีเสถียรภาพ รูปที่ 9 แสดงความสัมพันธ์ระหว่างอุณหภูมิการบำบัด HMDS และมุมสัมผัส (เวลาการบำบัด 60 วินาที) เมื่ออุณหภูมิสูงเกิน 120°C มุมสัมผัสจะลดลง แสดงว่า HMDS สลายตัวเนื่องจากความร้อน ดังนั้นการรักษา HMDS มักจะดำเนินการที่อุณหภูมิ 100-110 ℃
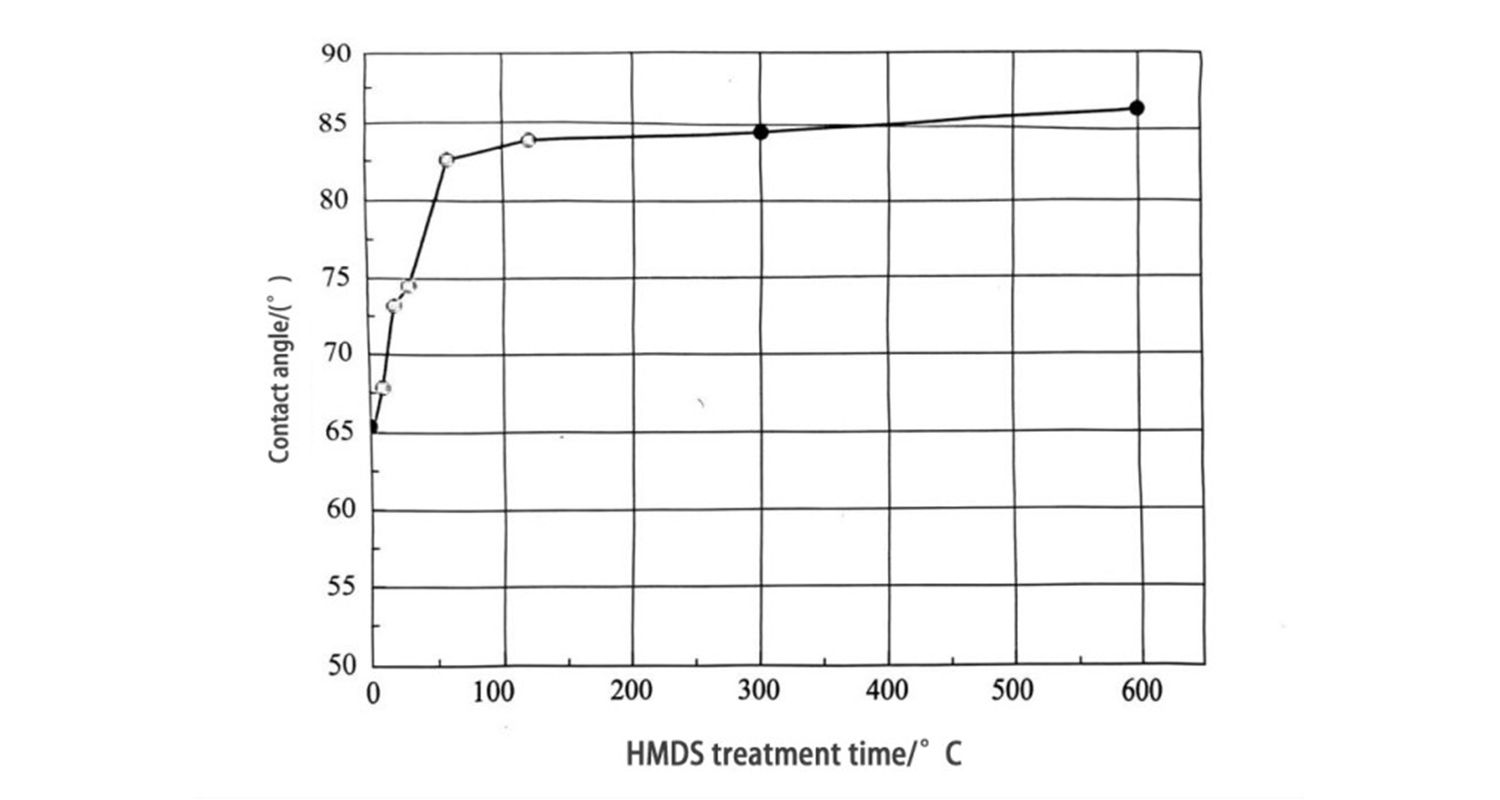
รูปที่ 8: ความสัมพันธ์ระหว่างเวลาการรักษา HMDS
และมุมสัมผัส (อุณหภูมิการรักษา 110 ℃)
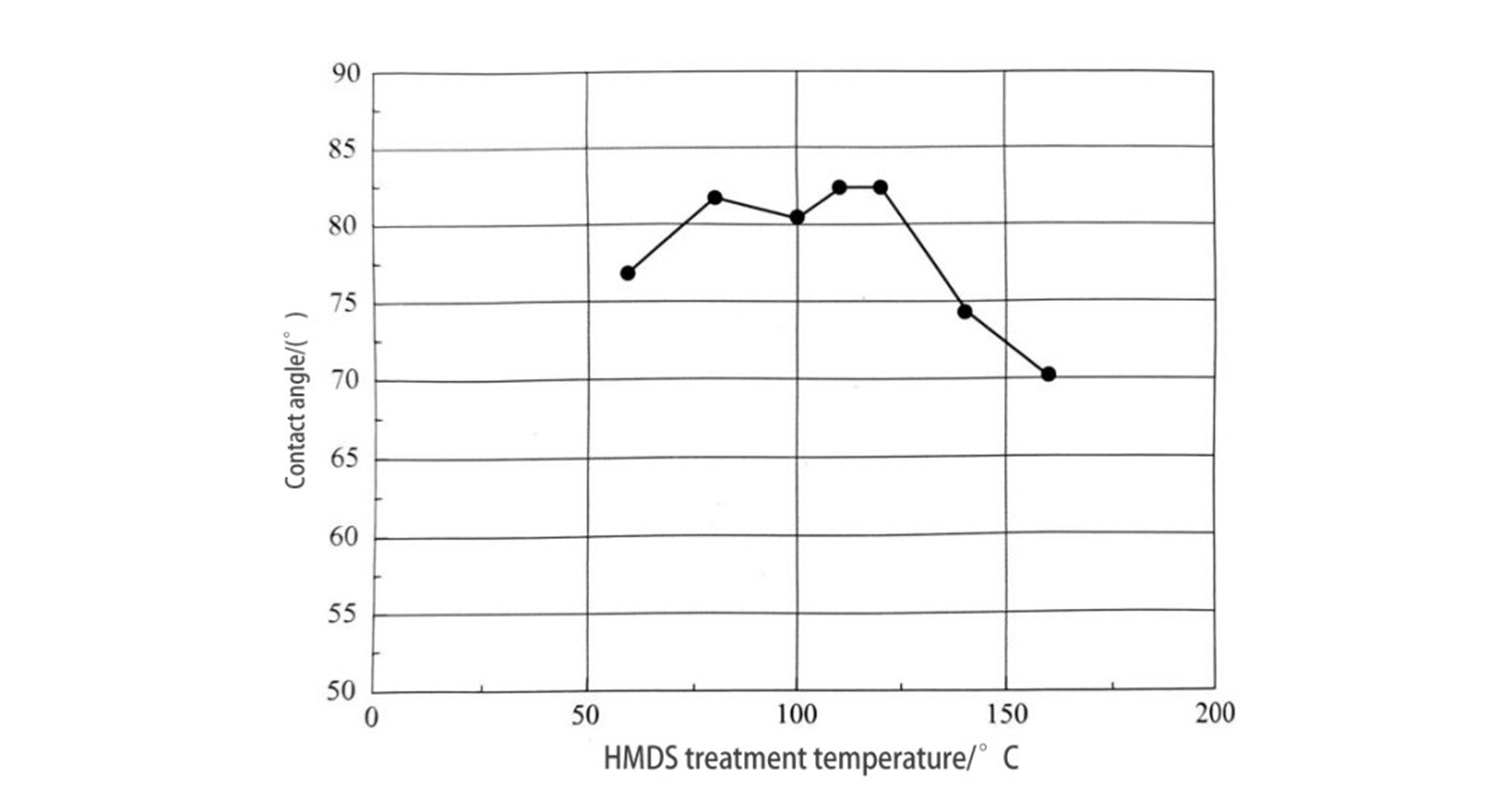
รูปที่ 9: ความสัมพันธ์ระหว่างอุณหภูมิการรักษา HMDS และมุมสัมผัส (เวลาการรักษา 60 วินาที)
การบำบัด HMDS ดำเนินการบนพื้นผิวซิลิกอนที่มีฟิล์มออกไซด์เพื่อสร้างรูปแบบไวแสง จากนั้นฟิล์มออกไซด์จะถูกแกะสลักด้วยกรดไฮโดรฟลูออริกโดยเติมบัฟเฟอร์ และพบว่าหลังการรักษาด้วย HMDS รูปแบบการต้านทานแสงสามารถป้องกันไม่ให้หลุดออกมาได้ รูปที่ 10 แสดงผลของการบำบัด HMDS (ขนาดรูปแบบคือ 1 ไมโครเมตร)
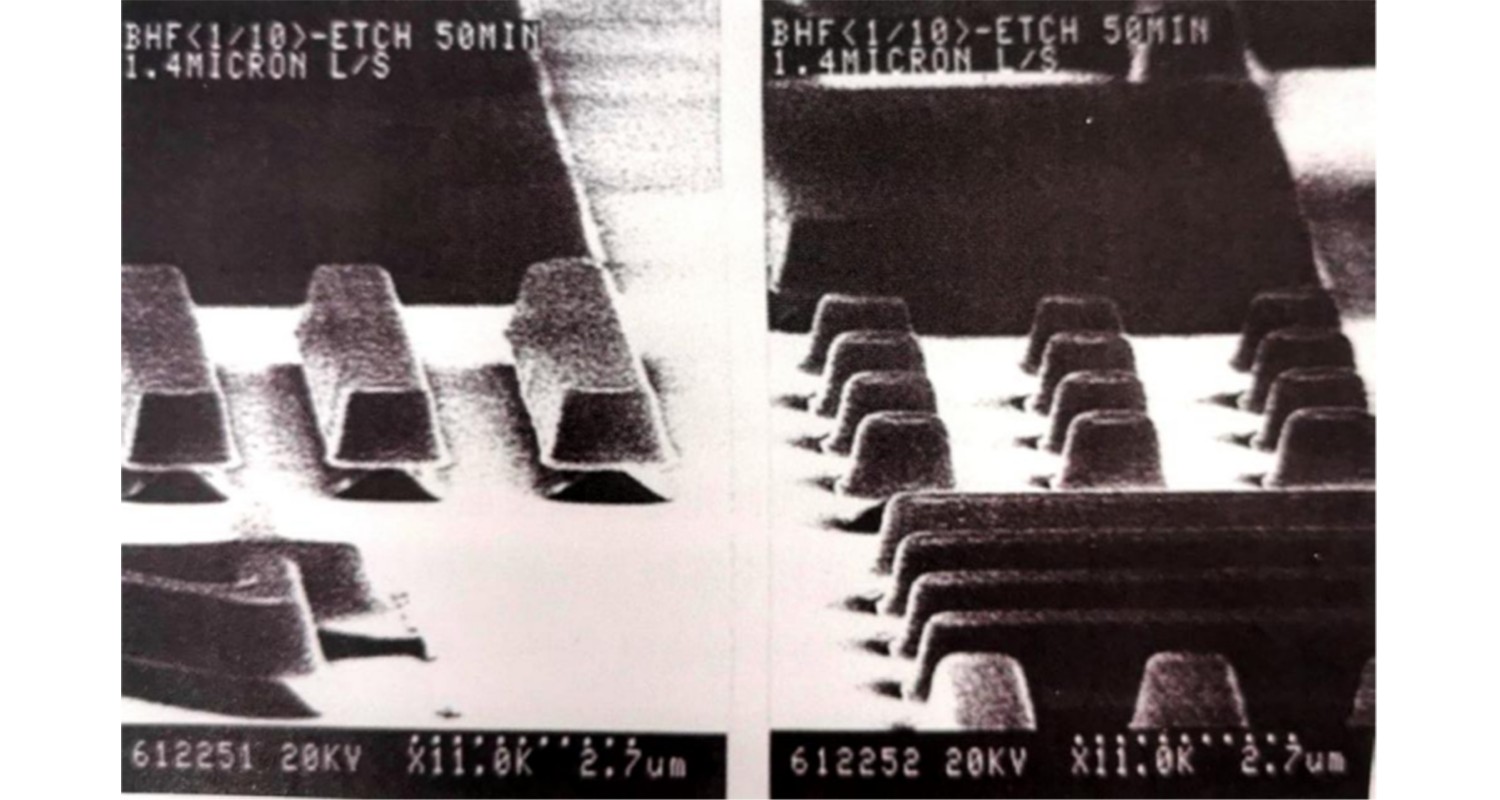
รูปที่ 10: ผลการรักษา HMDS (ขนาดรูปแบบคือ 1um)
กำลังเตรียมอบ
ที่ความเร็วการหมุนเท่ากัน ยิ่งอุณหภูมิเตรียมการอบสูงเท่าไร ความหนาของฟิล์มก็จะยิ่งน้อยลงเท่านั้น ซึ่งบ่งชี้ว่ายิ่งอุณหภูมิเตรียมการสูงขึ้น ตัวทำละลายก็จะระเหยออกไปมากขึ้น ส่งผลให้ความหนาของฟิล์มบางลง รูปที่ 11 แสดงความสัมพันธ์ระหว่างอุณหภูมิก่อนอบกับพารามิเตอร์ A ของ Dill พารามิเตอร์ A ระบุความเข้มข้นของสารไวแสง ดังที่เห็นได้จากรูปภาพ เมื่ออุณหภูมิก่อนอบเพิ่มขึ้นถึงสูงกว่า 140°C พารามิเตอร์ A จะลดลง ซึ่งบ่งชี้ว่าสารไวแสงจะสลายตัวที่อุณหภูมิสูงกว่านี้ รูปที่ 12 แสดงการส่งผ่านสเปกตรัมที่อุณหภูมิก่อนการอบที่แตกต่างกัน ที่อุณหภูมิ 160°C และ 180°C การส่งผ่านแสงที่เพิ่มขึ้นสามารถสังเกตได้ในช่วงความยาวคลื่น 300-500 นาโนเมตร นี่เป็นการยืนยันว่าสารไวแสงถูกอบและสลายตัวที่อุณหภูมิสูง อุณหภูมิก่อนอบจะมีค่าที่เหมาะสมที่สุด ซึ่งพิจารณาจากลักษณะเฉพาะของแสงและความไว
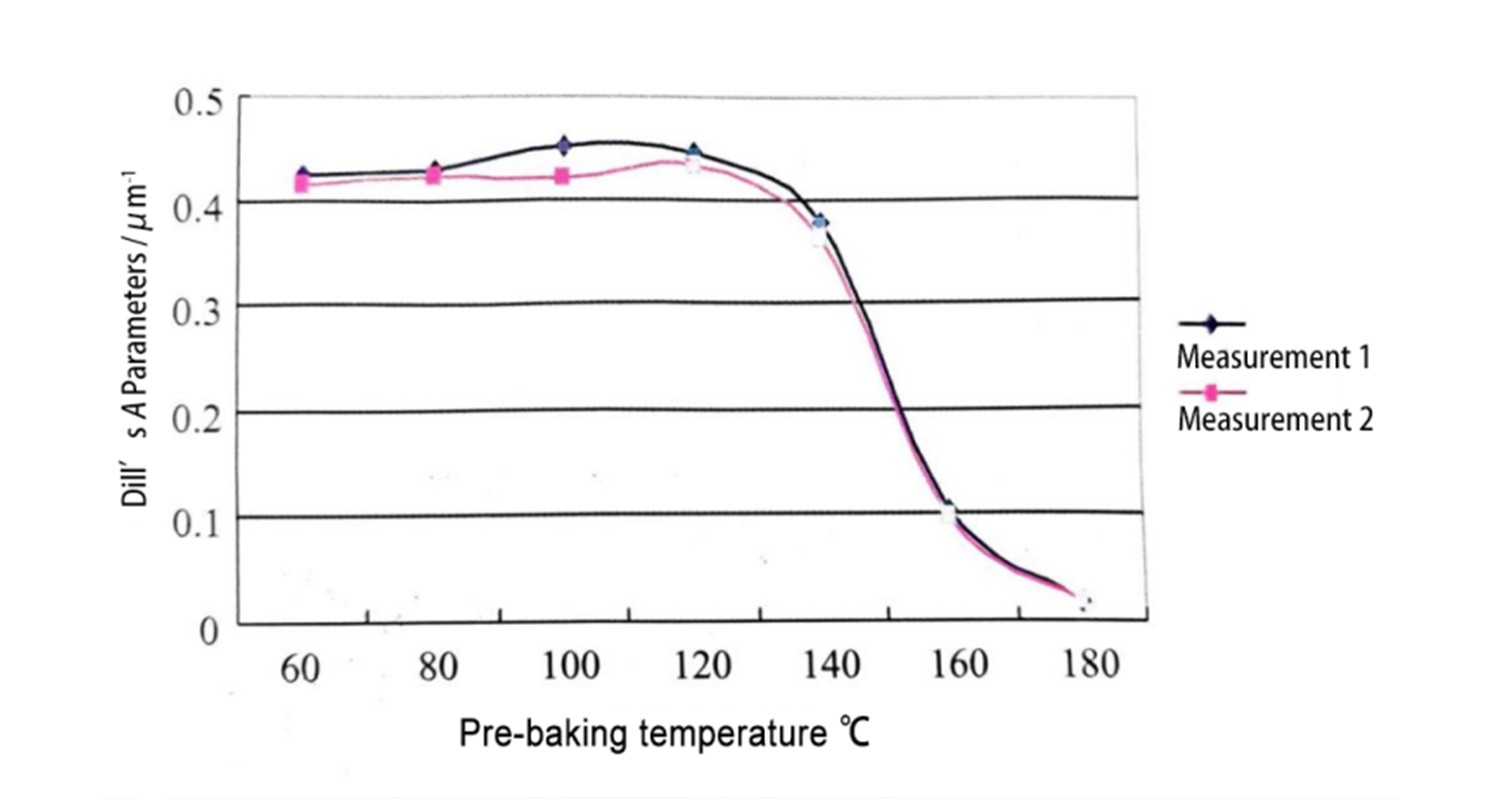
รูปที่ 11: ความสัมพันธ์ระหว่างอุณหภูมิก่อนอบกับพารามิเตอร์ A ของ Dill
(ค่าที่วัดได้ OFPR-800/2)
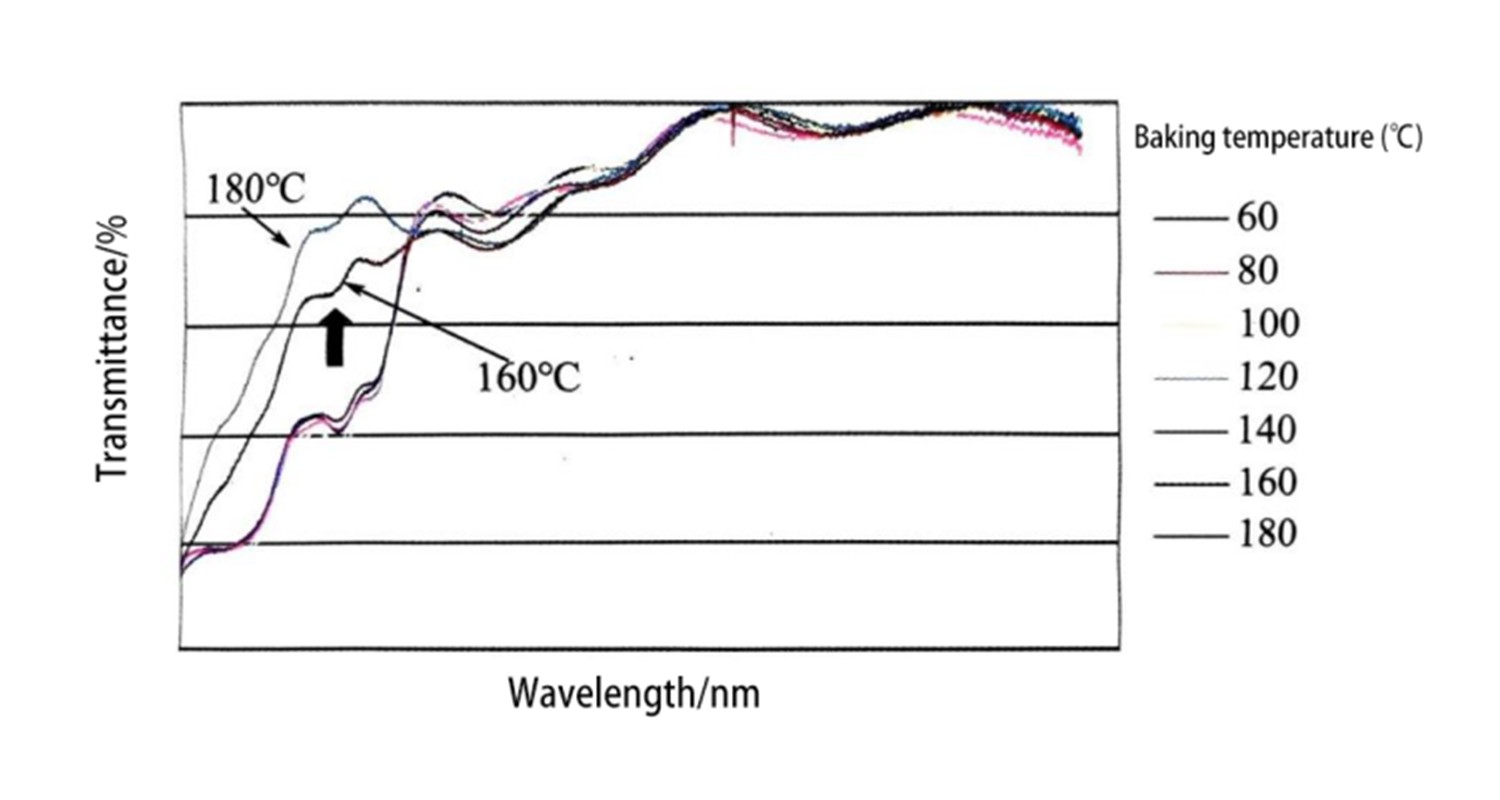
รูปที่ 12: การส่งผ่านสเปกตรัมที่อุณหภูมิก่อนการอบที่แตกต่างกัน
(OFPR-800, ความหนาของฟิล์ม 1um)
กล่าวโดยสรุป วิธีการเคลือบแบบหมุนมีข้อดีเฉพาะตัว เช่น การควบคุมความหนาของฟิล์มอย่างแม่นยำ ประสิทธิภาพด้านต้นทุนสูง สภาวะกระบวนการที่ไม่รุนแรง และการใช้งานที่เรียบง่าย ดังนั้นจึงมีผลกระทบอย่างมากในการลดมลภาวะ การประหยัดพลังงาน และปรับปรุงประสิทธิภาพด้านต้นทุน ในช่วงไม่กี่ปีที่ผ่านมา การเคลือบแบบหมุนได้รับความสนใจเพิ่มมากขึ้น และการประยุกต์ใช้งานก็ค่อยๆ แพร่กระจายไปยังสาขาต่างๆ
เวลาโพสต์: 27 พ.ย.-2024